以下是关于工厂生产车间安全管理培训的核心内容整合,结合最新行业规范及安全管理实践,分模块进行结构化阐述:
一、安全认知与责任体系
1. 安全意识重塑
安全不仅是制度要求,更是对生命价值的尊重。需通过事故案例逆向分析(如机械伤害、化学品泄漏等),强化“安全第一”的思维模式。
引入“安全行为银行”概念,将规范操作转化为积分奖励,激励员工主动参与安全管理。
2. 责任体系构建
明确车间主任、班组长、岗位员工的三级责任链:
车间主任:负责风险数据库动态管理,组织应急演练,落实安全投入。
班组长:每日检查设备状态,监督作业流程合规性,制止“三违”行为。
岗位员工:掌握本岗位风险点及应急措施,如化学品操作中的泄漏处理步骤。
二、车间核心风险防控
1. 机械设备安全
操作规范:执行“三步确认法”(开机前检查、运行中监控、停机后维护),重点防范夹卷、切割等机械伤害。
防护装置:确保联锁装置、急停按钮有效,定期测试光栅、安全门等防护设施。
2. 电气安全管理
推行“电气五防”:防短路、防漏电、防过载、防误操作、防触电。要求非专业人员禁止带电维修,湿手操作设备需使用绝缘工具。
高风险区域(如配电室)设置双重绝缘标识,并配备漏电保护系统。
3. 化学品风险控制
实施“三定”管理:定置存放(分类分区)、定量存储(最小存量)、定人操作(持证上岗)。
配备应急冲洗设施(如洗眼器、紧急喷淋),定期开展泄漏应急模拟演练。
4. 高处与受限空间作业
高处作业执行“三检”(安全带、踏板、护栏)和“双人监护”制度;受限空间作业前需进行气体检测,通风时间不少于30分钟。
三、安全培训与应急能力提升
1. 沉浸式培训设计
采用AR/VR技术模拟事故场景(如火灾逃生、设备故障),通过神经反馈技术监测学员应激反应,优化培训效果。
引入“岗位安全沙盒”,允许员工在虚拟环境中反复演练高风险操作(如起重机吊装),系统自动生成行为分析报告。
2. 应急预案与演练
制定“三级响应”机制:班组级(10分钟内处置)、车间级(30分钟联动)、厂级(1小时全员疏散)。
每季度开展盲演(无预警演练),测试应急通讯、逃生路线、伤员转运等环节的实效性。
四、安全检查与持续改进
1. 动态风险识别
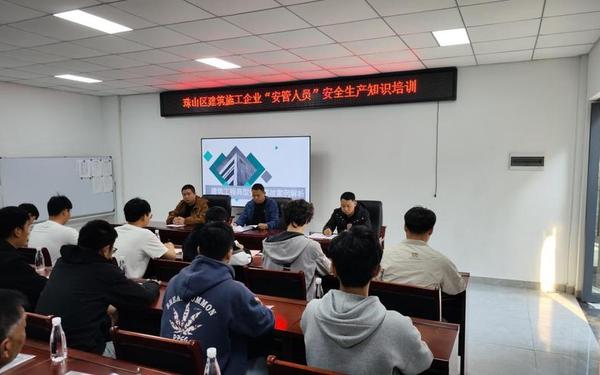
运用鱼骨图分析法,从“人、机、环、管”四维度识别风险点,如新员工技能不足、设备老化等。
建立“红橙黄蓝”风险分级管控台账,高风险项需车间主任签字确认整改方案。
2. 智能化巡检工具
推广智能工装(如防爆智能手环),实时监测员工位置、心率及环境数据(如氧气浓度),异常时自动报警。
利用AI摄像头识别违规行为(如未戴护目镜),同步推送至管理终端。
五、文化塑造与长效机制
1. 安全文化渗透
设立“安全之星”评选,鼓励员工提报隐患和改进建议;通过安全漫画、微电影等形式传播安全价值观。
推行“家庭共保”计划,邀请家属参与安全培训,构建“企业-家庭”双重监督网络。
2. 法规与标准更新
定期解读最新法规(如2025年《车间安全风险管理实施办法》),调整内部操作规程。
每半年开展安全合规性审计,确保制度与国标、行标同步。
通过以上模块化培训体系,可实现从“被动合规”到“主动防控”的转变,全面提升车间安全管理的系统性和实效性。建议企业结合自身行业特点(如化工、机械制造),定制化培训内容,并通过数字化工具持续追踪培训效果。