一、仓库管理制度
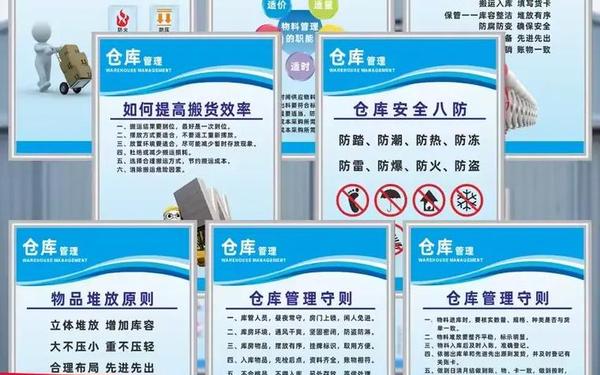
1. 入库管理
验收流程:所有物料入库需经质量部检验合格,核对送货单、采购合同及报检单,确保品名、规格、数量一致,并在入库单上签字确认。
单据管理:入库单分为《外购入库单》和《成品入库单》,需存档并分送财务、采购等部门。
异常处理:若发现数量不符或质量问题,仓库需拒收并立即通知相关部门。
2. 储存管理
分类存放:按物料属性、用途分区存放,实行“五五堆放”原则(五件一组、五组一排),标识清晰。
环境控制:保持仓库温湿度适宜(温度5~35℃,湿度40~85%),定期记录《仓库温湿度点检表》。
安全管理:禁止烟火,易燃易爆品单独存放并标识;通道畅通,货架摆放遵循“上轻下重、上小下大”原则。
3. 出库管理
领料流程:领料需填写领料单,经部门负责人和仓库主管审批后发放,遵循“先进先出”原则。
工具管理:工具领用以旧换新,记录于个人工具卡;借用工具需登记台账,逾期未还需扣罚折旧费。
发货跟踪:仓库需核对发货单信息(品名、数量、质量),跟踪物流至客户签收。
4. 盘点与账务
定期盘点:每月中小盘,年末大盘,做到账、卡、物一致;盘点结果报财务部。
账务处理:每日登记台账,单据按月装订存档,定期与财务对账。
报废管理:报废物资需填写《报废申请单》,经质量部、财务部审核后处理,价值超万元需总经理审批。
5. 其他要求
5S管理:执行整理、整顿、清扫、清洁、素养、安全、节约原则。
交接制度:仓管员离职需完成账务和实物交接,确认无误后方可离岗。
二、车间管理制度
1. 生产物资管理
领料规范:按生产计划领料,超领需审批;补料需填写补料单并说明原因。
退料流程:剩余物料需填写《退料单》,经质检合格后退回仓库,冲减原领料记录。
工具使用:工具借用需登记台账,损坏或遗失需赔偿;大型工具由班组长统一管理。
2. 现场管理
设备维护:定期保养设备,故障设备需标识并隔离,避免混用。
5S执行:保持车间整洁,物料按区域分类存放,通道无杂物。
安全管理:操作人员需佩戴劳保用品,危险作业需审批并设置警示标识。
3. 质量控制
首件检验:每批生产前需检验首件产品,合格后方可批量生产。
过程监控:质检员巡检生产流程,记录异常并整改;不合格品隔离存放。
4. 人员管理
培训制度:新员工需接受岗前安全及操作培训,考核合格后上岗。
考勤纪律:严禁迟到早退,请假需提前申请;违规操作纳入绩效考核。
三、岗位职责
1. 仓库岗位
仓管员:负责收发料、日常盘点、台账登记及仓库安全。
记账员:管理单据和账目,定期输出报表,配合财务抽查账实一致性。
仓库主管:监督仓储规划、库存管控、制定管理制度及协调跨部门沟通。
2. 车间岗位
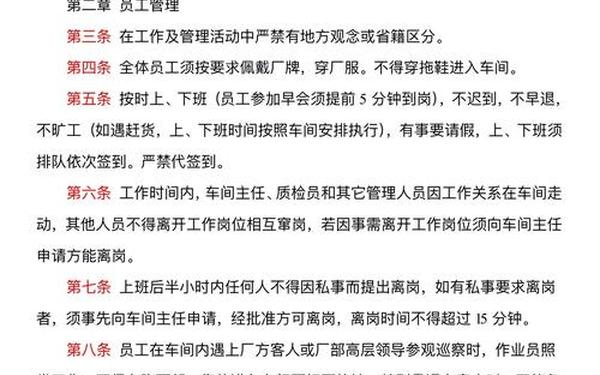
车间主任:统筹生产计划执行、现场管理及人员调度。
班组长:监督本组生产进度、质量及安全,协调物料领用。
质检员:负责原材料、半成品和成品的质量检验,记录并反馈问题。
四、违规处理
仓库:未按流程操作导致损失,按情节扣罚工资;私自处理报废物资视为违纪。
车间:违规操作引发事故,追究当事人及主管责任;物料浪费按成本扣罚。
以上制度综合了入库、储存、出库、盘点等全流程规范,以及车间生产、质量、现场管理的核心要求,引用自多篇权威资料。实际执行中需结合企业具体情况调整,并定期培训员工以确保落地。