以下是关于生产安全知识培训及车间安全生产管理的综合总结,结合法律法规、管理策略和实操案例,提供系统化的解决方案:
一、生产安全知识培训的核心内容
1. 基础安全理论
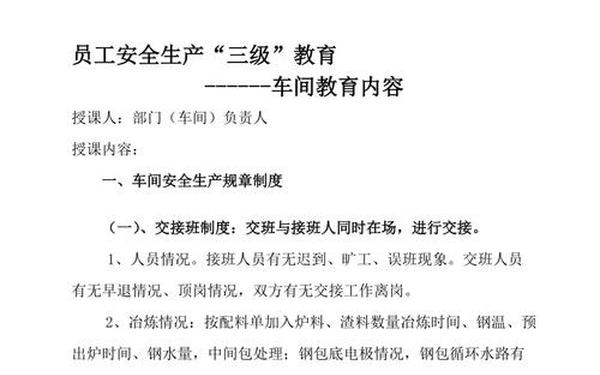
安全定义与原则:安全生产是通过科学管理和技术措施保障人身、财产和环境安全,遵循“安全第一、预防为主、综合治理”的原则。
事故根源:包括人的不安全行为(如违章操作)、物的不安全状态(设备故障)及管理缺陷。
“三不伤害”原则:不伤害自己、不伤害他人、不被他人伤害。
2. 车间安全操作规范
电气安全:禁止私接电路,设备接地/接零,湿手不操作电器,定期检查线路。
机械安全:设备操作前检查,停机维修时挂警示牌,禁止戴手套操作旋转设备。
化学品管理:分类存放、标识清晰,泄漏时立即通风并报告,佩戴防护用品。
高空作业:使用安全带和防滑梯具,禁止抛掷工具,设专人监护。
3. 应急处理能力
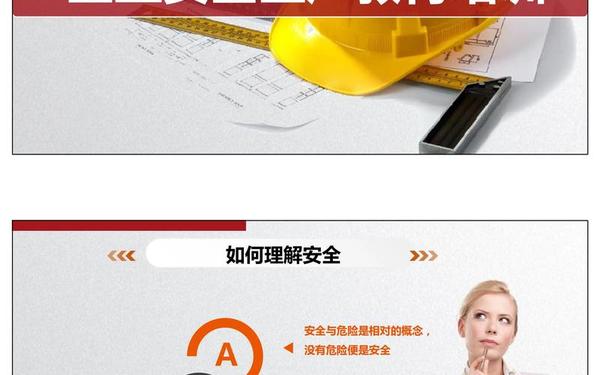
火灾应对:使用灭火器(干粉、二氧化碳)、疏散逃生路线演练。
触电急救:切断电源后施救,禁止直接接触触电者。
心肺复苏(CPR):培训员工掌握急救流程,提高黄金救援时间成功率。
二、车间安全生产管理的关键策略
1. 三级安全教育体系
厂级教育:企业概况、安全法规、事故案例警示。
车间教育:区域风险点(如高温设备、化学品存放)、设备操作规程。
班组教育:岗位操作细节、防护用品使用、隐患排查方法。
2. 风险管控与隐患排查
风险评估工具:采用风险矩阵法,识别高风险作业(如动火、吊装)并分级管控。
日常检查机制:班前设备点检、班中行为监督、班后交接记录。
整改闭环:隐患登记→责任到人→限期整改→复查验收。
3. 科技赋能安全管理
物联网监测:实时监控设备运行状态,预警异常数据。
VR模拟培训:通过虚拟场景演练事故应急,提升员工应对能力。
数字化台账:使用安全管理软件记录培训、检查、事故等数据,便于追溯。
三、成功实践案例与经验
1. 案例1:深圳某光电公司安全培训
模块化课程设计:分设隐患排查、化学品管理、设备操作等专项培训,结合实操演练提升技能。
成果:员工隐患识别率提高40%,事故率下降25%。
2. 案例2:杜邦安全管理模式借鉴
行为观察法:管理人员定期观察员工操作,纠正不安全行为并反馈。
安全绩效指标:将事故率、整改率与部门考核挂钩,强化责任落实。
3. 案例3:某制造企业安全文化构建
全员参与机制:设立安全提案奖励,鼓励员工上报隐患。
文化渗透活动:安全月竞赛、家庭安全日,提升员工及家属安全意识。
四、制度与责任落实
1. 安全生产责任制
管理层责任:车间主任为安全第一责任人,制定年度安全计划并监督执行。
员工职责:遵守操作规程、参与培训、报告隐患、配合事故调查。
2. 考核与奖惩机制
四不放过原则:事故原因未查清不放过、责任人未处理不放过、整改未落实不放过、全员未受教育不放过。
动态考核:月度安全评分与绩效奖金挂钩,重大违规“一票否决”。
五、未来趋势与挑战
智能化升级:AI算法预测设备故障,无人机巡检高风险区域。
心理安全建设:关注员工心理健康,减少因压力导致的误操作。
法规动态适应:紧跟《安全生产法》修订,调整企业安全策略。
通过系统化的培训、科技手段的应用及责任制度的完善,企业可显著提升车间安全管理水平。建议定期更新培训内容(参考网页1、67),结合案例实践(如网页45)优化管理流程,最终实现“零事故”目标。