以下是针对工厂安全生产的合理化建议和改善提案,结合安全管理、技术优化、文化培育等多个维度,综合整理如下:
一、安全管理体系优化
1. 强化责任制度
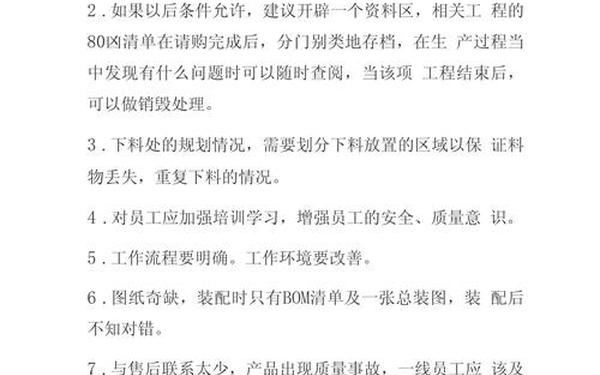
落实“管行业必须管安全、管业务必须管安全、管生产经营必须管安全”的“三管三必须”原则,明确各级负责人为安全生产第一责任人,建立全员安全生产责任制。
定期开展安全风险评估,通过“人、机、料、境、法”五要素分析,制定风险分级管控措施。
2. 规范隐患排查与整改
建立双重预防机制(安全风险分级管控和隐患排查治理),定期检查设备老化、线路混乱、消防设施缺失等问题,并通过信息化系统动态追踪整改进度。
推行“零容忍”隐患管理,例如禁止车间存放易燃油桶、规范取暖设备使用等。
二、生产现场管理提升
1. 5S标准化管理
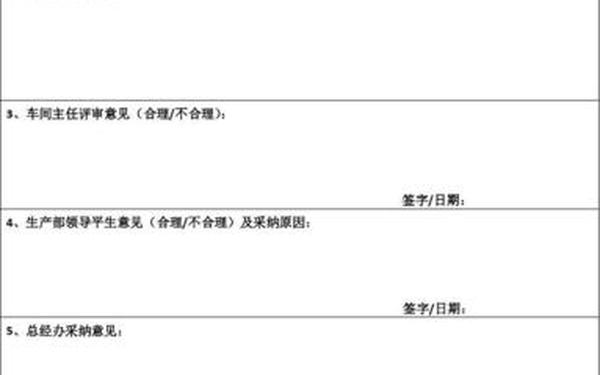
推行整理(Seiri)、整顿(Seiton)、清扫(Seiso)、清洁(Seiketsu)、素养(Shitsuke)的5S管理,确保工作区域物件摆放有序、道路畅通,减少因环境混乱导致的安全事故。
定期清理车间更衣室、设备区,避免杂物堆积引发火灾或绊倒风险。
2. 设备与工艺改进
更新老化设备,引入自动化生产线和智能监控系统(如物联网传感器),实时监测设备运行状态,预防机械故障。
优化工艺流程,减少非必要操作步骤,例如通过数据分析和精益生产降低人为操作风险。
三、安全教育培训创新
1. 多样化教育形式
开展“每周一案”“每日一题”活动,利用真实事故案例制作视频或动画,通过微信、广播等渠道进行传播,增强员工代入感。
对新员工实施“三级安全教育”(公司、车间、班组),考核合格后方可上岗;对特种作业人员(如电工、叉车司机)强化持证培训。
2. 互动式培训与考核
组织安全知识竞赛、应急演练,模拟火灾、机械伤害等场景,提升员工应急处置能力。
建立安全考试系统,不合格者需停工学习,通过经济手段(如全员安全奖挂钩)强化责任意识。
四、技术创新与信息化应用
1. 智能化安全监控
部署SASE(安全访问服务边缘)架构,保护工厂网络免受勒索软件攻击,同时实现生产数据的安全传输。
利用AI和大数据分析预测设备故障,例如通过振动传感器监测机床异常,提前维修避免停机。
2. 应急管理系统建设
建立数字化应急预案,整合消防、医疗等资源,实现事故一键报警和快速响应。
在关键区域设置智能安全标识(如电子围栏、声光报警),动态提示危险区域。
五、安全文化与企业氛围
1. 全员参与机制
设立“安全积分”奖励制度,鼓励员工举报隐患、提出改善提案,对贡献突出者给予物质或荣誉奖励。
开展“安全之星”评选,通过榜样力量带动团队重视安全。
2. 领导示范与透明管理
管理层定期参与车间安全检查,公开安全绩效(如事故率、整改率),增强员工信任感。
建立匿名安全意见反馈渠道,确保员工敢于发声。
六、合规与法律保障
1. 遵守《安全生产法》要求
确保安全投入(资金、物资、人员)到位,定期更新防护用品(如绝缘鞋、防毒面具)。
依法编制安全生产权力和责任清单,接受社会监督。
通过制度完善、技术创新、文化培育三管齐下,工厂可构建“预防为主、全员参与、持续改进”的安全管理体系。建议优先从设备维护、5S管理、教育培训等易见效的领域切入,逐步向智能化、数字化转型,最终实现安全生产与效率提升的双重目标。具体措施可参考《安全生产法》及相关行业标准,并结合企业实际灵活调整。