以下是关于6S管理的心得体会与感悟总结,结合理论框架与实践案例,涵盖整理、整顿、清扫、清洁、素养、安全六大核心要素:
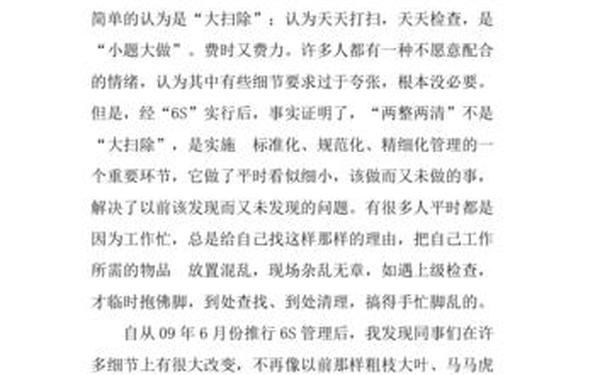
一、环境改善与效率提升
1. 从“脏乱差”到井然有序
通过整理(SEIRI)和整顿(SEITON),清除不必要的物品,对必需品进行科学分类和标识,工作现场从杂乱无章转变为整洁高效。例如,某工厂通过整理工具和物料,减少寻找时间30%,生产效率提升20%。
在医疗场景中,手术室通过定位管理无菌物品和设备,显著缩短术前准备时间,降低感染风险。
2. 清扫(SEISO)与清洁(SEIKETSU)的持续作用
定期清扫不仅保持环境整洁,还能发现设备隐患。例如,某车间通过每日设备点检,避免因机械故障导致的停工。
清洁的标准化制度(如文件归档规范、物料摆放标准)形成长效管理机制,减少“反弹”现象。
二、素养提升与文化塑造
1. 从被动执行到主动参与
6S管理的核心在于素养(SHITSUKE)。通过制度约束和激励措施,员工逐渐养成规范操作、自觉维护环境的习惯。例如,某企业将6S表现纳入绩效考核后,员工违规率下降50%。
医院护士站通过目视化标签和收纳工具,实现文件、物品的快速定位,潜移默化中培养员工的责任感和细致度。
2. 安全(SECURITY)意识的深化
安全不仅是硬件防护,更需融入日常行为。某车间通过规范电线收纳和工具存放,消除绊倒、误触等隐患,事故率降低80%。
在食品企业中,6S管理结合食品安全流程(如原料检验、操作规范),保障“舌尖上的安全”。
三、管理思维与组织变革
1. 数据化与标准化驱动管理升级
通过统计生产数据(如不良品率、设备故障率),企业精准定位问题,优化流程。例如,某工厂引入6S后,物料浪费减少15%,库存周转率提升10%。
标准化操作手册和可视化看板(如设备维护流程、安全警示图)成为新员工培训的核心工具。
2. 从局部试点到全员推广
成功的6S管理需循序渐进。某企业选择样板区先行试点,积累经验后全面铺开,避免“一刀切”导致抵触情绪。
通过竞赛、评比激发团队荣誉感,例如某医院开展科室6S评比后,患者满意度提升25%。
四、持续改进与挑战
1. 避免“运动式”管理
6S需长期坚持,部分企业初期效果显著,但因缺乏制度固化而“昙花一现”。例如,某车间通过定期稽核和奖惩机制,将6S融入日常管理,形成可持续文化。
2. 技术与管理的融合
数字化工具(如智能仓储系统、电子巡检)助力6S高效落地。某仓库通过扫码定位物料,出入库效率提升40%。
结合精益生产、TPM等工具,形成综合管理体系,释放更大效益。
五、个人感悟与启示
细节决定成败:6S强调从小处入手,如办公桌的整理、工具的归位,看似简单却直接影响工作心态和效率。
以人为本的管理哲学:6S不仅是环境改造,更是对员工习惯和价值观的塑造。叶圣陶所言“习惯即能力”在此得到印证。
组织与个体的共赢:良好的环境提升员工归属感,企业形象与竞争力随之增强,形成良性循环。
总结:6S管理不仅是工具,更是思维变革的起点。通过环境改善、素养提升和制度优化,企业可实现效率、安全、文化的全面升级。其核心在于坚持“PDCA循环”(计划-执行-检查-改进),将短期成果转化为长期竞争力。