一、生产管理核心流程
1. 订单接收与评估
接收客户订单并记录关键信息(订单号、产品规格、数量等),进行初步产能评估。
重点审核交期、技术要求和特殊需求,确认是否需调整生产资源。
2. 生产计划制定
根据订单需求、设备能力和原材料库存制定详细计划,平衡产能与交期。
考虑设备利用率、人员排班、供应链协同等,避免资源浪费。
3. 原材料采购与检验
按计划采购原材料,严格遵循供应商评估和合同规范。
执行进厂检验制度,包括取样检测、质量证明书核验,不合格材料需技术部和品管部联合处理。
4. 生产执行与现场管理
实施标准化操作(SOP),动态监控设备状态、物料流转及员工操作。
通过日报表跟踪进度,及时调整瓶颈工序,确保按时交付。
5. 质量管控与出厂检验
设立过程检验点(如首检、巡检),确保产品符合国家标准或客户要求。
成品需经理化实验室检测,批次合格后签发报告方可出厂。
6. 交付与售后服务
产品入库后快速安排物流,记录客户反馈并纳入改进机制。
二、制度框架与核心要求
1. 质量管理制度
建立ISO9001体系,覆盖设计、采购、生产、检验全流程,通过内审和管理评审持续改进。
推行“零缺陷”目标,明确质量红线,如不合格品隔离与追溯。
2. 设备与资源管理制度
实施TPM(全面生产维护),制定设备保养基准书,预防故障并提升效率。
推行5S管理,优化车间布局,减少物料积压和搬运浪费。
3. 安全管理制度
落实安全生产标准化,定期开展安全培训、应急演练及隐患排查。
重点区域(如危化品存储)需设置警示标识,严格动火作业审批。
4. 人员与绩效制度
实行技能分级认证,通过培训提升员工操作规范性。
绩效考核与质量指标、效率提升挂钩,设置改进提案奖励机制。
三、优化与创新方向
1. 数字化与智能化升级
引入MES系统实时监控生产数据,利用AI预测设备故障。
搭建供应链协同平台,优化采购周期与库存周转。
2. 流程标准化与持续改进
制定SOP文件,明确各环节操作规范,定期修订更新。
通过PDCA循环(计划-执行-检查-处理)推动问题闭环。
3. 绿色与可持续发展
推行ISO14001环境管理体系,减少能耗与废弃物排放。
探索循环经济模式,如废料回收再利用。
四、常见问题解决方案
交期延误:通过动态排程工具优化生产节奏,加强供应链备货预警。
成本过高:分析浪费根源(如过度加工、库存冗余),实施精益生产。
质量波动:运用SPC(统计过程控制)监控关键参数,及时调整工艺。
引用来源:
以上流程与制度可根据企业规模(如小作坊或大型工厂)灵活调整,建议结合ISO认证和行业特性细化实施。
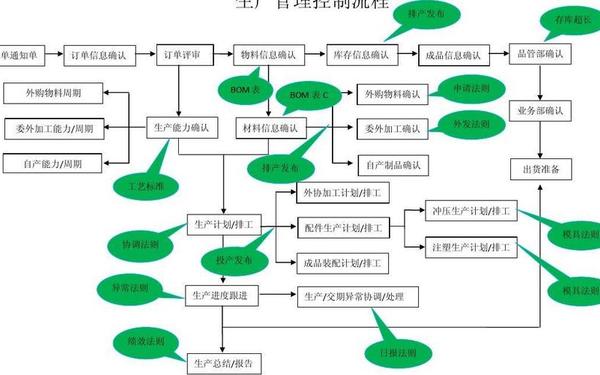