以下是针对涂装车间及生产车间的改善提案精选,结合安全管理、效率提升、质量优化、设备维护等多个维度,提供可落地的改善方向,并附参考案例及来源:
一、安全管理优化
1. 危化品储存规范
使用桶装替代袋装保险粉,避免泄漏风险;危化品仓库增设防护栏和警示标志,设置专用防爆储存区。
案例:某印染企业通过规范危化品储存,年减少事故率30%。
2. 设备安全防护
砂轮机加装软垫和托盘装置,防止金属飞溅;高温区域设置红色斑马线警示区,禁止非作业人员靠近。
案例:某车间通过增设砂轮机防护装置,工伤率下降50%。
3. 消防与应急管理
定期检查灭火器有效期,每月开展消防演练;仓库顶部漏水处用沥青修补,围墙根部建排水沟防积水。
案例:某企业通过消防器材标准化配置,应急响应时间缩短至3分钟。
二、效率提升与流程优化
1. 快速换模(SMED)
标准化换模流程,通过预调参数和并行操作,将换模时间从45分钟缩短至8分钟。
案例:某冲压车间通过SMED实现换模效率提升5倍。
2. 目视化与标准化作业
使用形迹管理工具(如磁性工具墙),5秒内定位工具;地面标记设备移动轨迹,减少搬运距离。
案例:某维修车间通过工具形迹管理,工具丢失率降低80%。
3. 生产节拍优化
按车型颜色分组生产,减少换色清洗频率;优化空调开关机时间,利用谷电蓄冷降低能耗。
案例:某涂装车间通过分组生产,溶剂消耗减少25%。
三、质量与工艺改进
1. 防错工装设计
采用限位块和环状喷头设计,防止漏装或喷涂不均;关键螺栓扭矩标记,确保装配一致性。
案例:某发动机装配线通过防错工装,漏装率降至0.1%。
2. 质量门控制
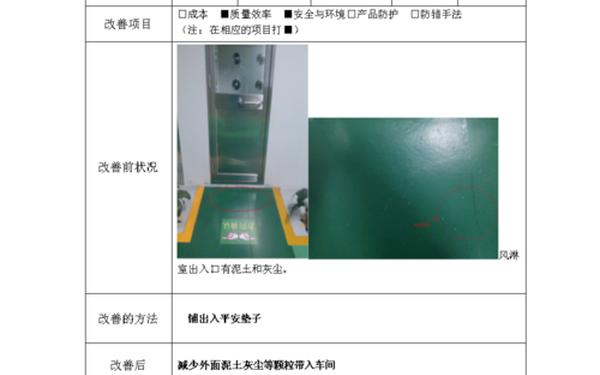
关键工序设质量拦截点(如涂装线出口色差比对),不合格品立即隔离并追溯责任人。
案例:某车间通过质量门制度,返工率下降40%。
3. 工艺参数监控
实时记录喷涂参数(温度、湿度、膜厚),利用AI分析预测涂层缺陷。
案例:某企业通过参数监控系统,面漆合格率提升至98%。
四、设备与能源管理
1. 预防性维护
建立设备润滑路线图(如机床35个润滑点每月循环),利用振动分析预测轴承磨损。
案例:某车间通过预防性维护,设备故障率降低60%。
2. 余热回收与节能改造
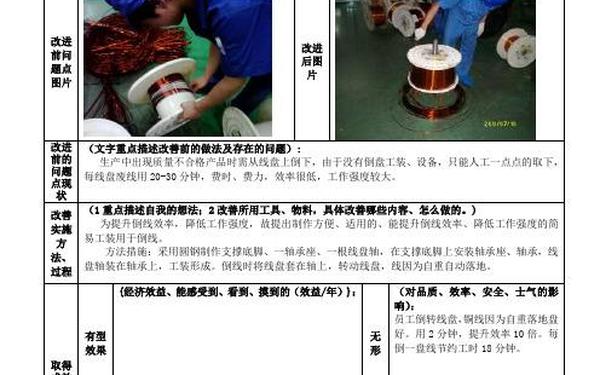
空压机余热用于车间供暖,谷电蓄冷降低空调能耗;淘汰高耗能设备,更换高效空压机。
案例:某企业通过余热回收项目,年节约电费190万元。
3. 智能诊断系统
引入AI分析设备运行数据,预测刀具寿命(准确率92%);二维码点检替代纸质记录,漏检率降至0.2%。
案例:某车间通过智能诊断,设备OEE从65%提升至85%。
五、员工参与与文化建设
1. 提案奖励机制
设立改善提案看板,按效果分级奖励(一等奖2000元至鼓励奖5元),定期展示优秀案例。
案例:某车间通过员工提案,年节省成本超50万元。
2. 多能工培养
建立技能矩阵图,开展AR眼镜辅助培训,新员工培训周期缩短50%。
案例:某注塑车间通过多能工轮岗,人员调配效率提升30%。
3. 安全文化渗透
每日广播播放安全知识,每周剖析事故案例;管理层定期参与班组安全讨论。
案例:某企业通过安全教育常态化,违章操作减少70%。
六、环保与可持续改进
1. “三废”管理
分类回收废漆渣、溶剂,引入水性涂料替代溶剂型涂料;废水处理系统增设PH值实时监控。
案例:某车间通过水性涂料改造,VOC排放减少90%。
2. 循环利用优化
废溶剂蒸馏提纯后回用,废包装桶清洗重复使用;旧砂轮回收用于低精度工序。
案例:某企业年节约危废处理费用80万元。
实施建议:
优先解决高风险问题(如危化品管理、消防隐患),再逐步推进效率与质量优化。
结合车间实际选择3-5项试点,成功后横向推广。
参考来源案例中的具体参数(如),制定详细执行计划。
更多完整案例可查阅相关来源网页,根据车间需求定制化调整方案。