以下是为企业制定的节能减排综合方案及车间节能降耗建议,结合政策导向与行业实践,涵盖管理机制、技术创新、设备优化等多维度措施:
一、公司整体节能减排方案
1. 组织架构与目标设定
成立领导小组:由总经理牵头,各部门负责人组成领导小组,负责制定节能目标、监督执行(如电信企业案例中设立节能减排工作小组)。
目标分解:参照国家《2024-2025年节能降碳行动方案》,设定单位产值能耗降低2.5%、碳排放强度下降3.9%等具体指标,按部门/车间分解任务。
2. 分领域实施措施
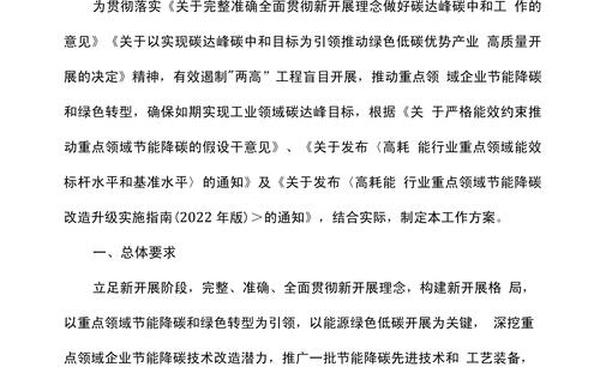
(1)能源结构优化
化石能源减量:淘汰35蒸吨以下燃煤锅炉,推广天然气替代;炼油、化工行业严格产能控制。
非化石能源提升:厂房屋顶安装分布式光伏,配套储能系统;余热发电项目(如钢铁行业余压发电技术)。
(2)重点领域改造
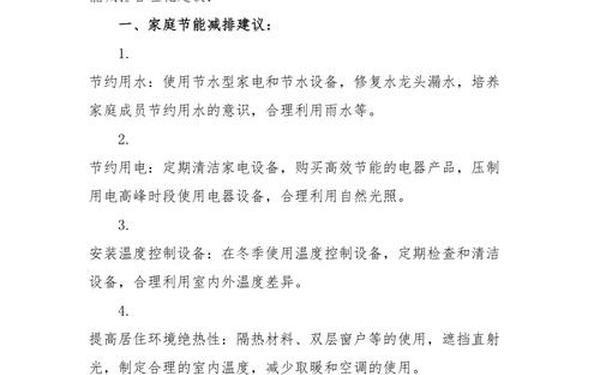
生产工艺升级:钢铁行业推广电炉短流程炼钢;石化行业实施能量系统优化;建材行业推广低碳原料替代。
设备能效提升:采用阿法拉伐高效板式换热器,减少工业流程能耗;数据中心应用自然冷却技术,降低空调用电。
(3)管理机制强化
数字化监测:安装智能电表、水表实时监控能耗,建立能源管控平台识别异常消耗。
考核激励:将节能指标纳入部门KPI,对提出有效建议的员工给予奖励(如合理化建议征集活动案例)。
二、工厂车间节能降耗具体建议
1. 生产流程优化
减少空转与等待:通过精益生产排程缩短设备闲置时间,如“一罐到底”铁水运输减少热能损失。
余热回收利用:在炼钢、注塑等高温工序加装余热锅炉,用于供暖或发电(参考钢铁行业环冷机改造案例)。
2. 设备管理升级
淘汰高耗能设备:替换IE3以下能效电机,推广变频控制技术(如冶金行业电机系统节能控制技术)。
定期维护保养:清洁空调滤网提升制冷效率,润滑生产线传动部件降低摩擦损耗。
3. 资源循环利用
废料再生:金属加工车间回收切削废料重熔;化工车间实施溶剂回收系统。
水资源循环:冷却水循环利用率提升至95%以上,废水处理后用于绿化或清洁。
4. 员工参与与培训
文化宣导:张贴节能标语,开展“节能标兵”评选,强化全员节约意识。
技能培训:组织设备操作规范培训,避免因误操作导致能源浪费。
5. 技术创新应用
多孔介质燃烧技术:用于干燥、热处理工序,比传统燃烧方式节能40%。
智能照明系统:车间安装光感+人体感应LED灯,无人区域自动关闭。
三、政策与技术支持
政策申报:参与碳普惠项目(如深圳高效制冷机房项目),获取核证减排量收益。
技术合作:与科研机构联合开发氢冶金、CCUS等前沿技术,争取补贴。
实施效果预估
通过上述措施,企业可实现:
直接效益:年节约电费15%-30%,减少碳排放20%以上(参考钢铁行业改造案例年减排CO₂万吨级)。
长期价值:符合ESG投资趋势,提升绿色供应链竞争力,规避环保政策风险。
数据来源:国务院及地方节能政策、工业节能技术指南、企业实践案例。建议结合企业实际需求选择适配措施,并持续跟踪改进。